OEM カスタム高精度プログレッシブ パンチング深絞り金型鋳造および板金金型スタンピング金型
ビデオ
関数
プログレッシブ ダイは、連続ダイとも呼ばれ、ダイには 2 つ以上のステーションがあり、異なるステーションで 2 つ以上のスタンピング プロセスを完了することができます。
応用分野
自動車部品の自動車産業。
自動車生産ラインの生産能力向上。
製品詳細
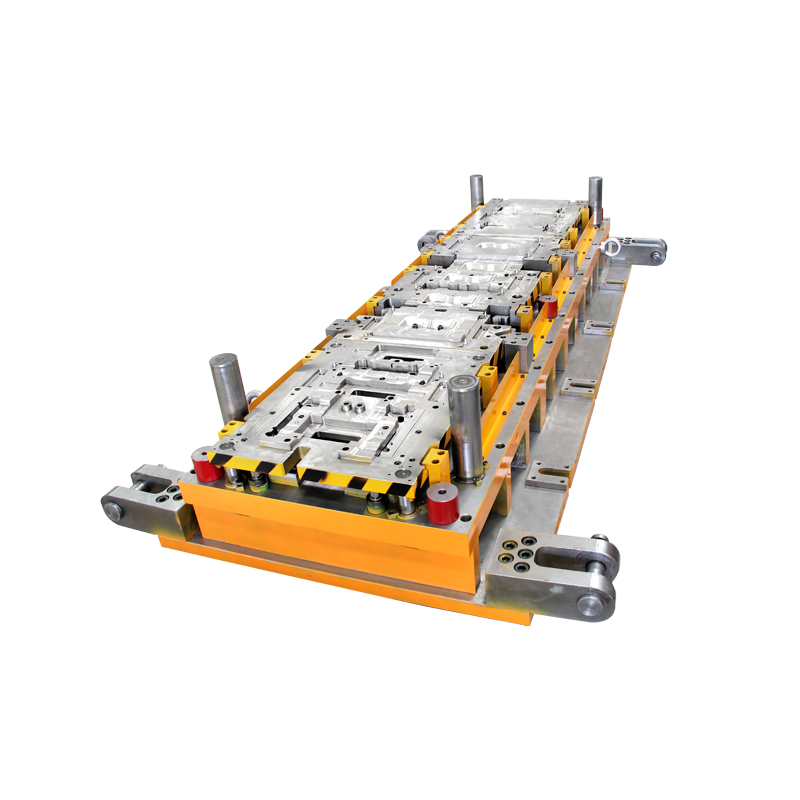
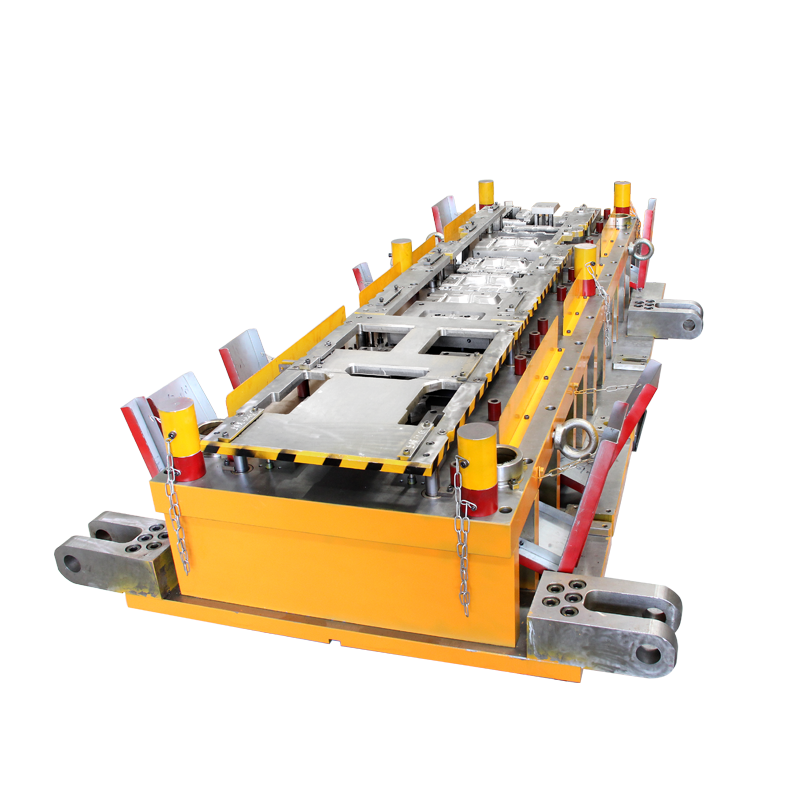
詳細な紹介
金型の設計作業の基本的な要件は次のとおりです。金型の設計は、図面から部品が形状とサイズの要件に沿っていることを保証する必要があります。金型の構造は簡単で、しっかりと取り付けられ、メンテナンスが便利で、耐久性があります。操作が簡単で、安全で信頼できる作業。製造が簡単、低価格。
金型設計の一般的な手順
まず、必要な情報を収集し、プレス工程を分析します。含む: 部品の形状、サイズ、精度の要件、およびアセンブリ関係の完全なビュー、技術要件の明確な図面またはサンプルが必要です。部品スタンピング工程カード(通常はスタンピング技術者から提供されます)を理解し、その前後を研究します。工程と加工工程要件との関係は、工程間で相互に保証されなければならず、金型の数と種類は、工程カードで指定された工程計画に従って決定されるものとします。部品の生産性(試作またはバッチまたは大量生産)をマスターして、金型構造を決定します。単純な金型またはより複雑な高生産金型を使用します。シート材料またはストリップ材料、ロール材料またはスクラップ材料などの構成材料の性質、サイズ、および供給方法を理解する。プレスと関連する技術仕様を理解し、選択した機器に応じて金型のアンロード方法とその他の補助手順を決定します。
金型製作の技術力、設備条件、加工技術を理解し、金型の構造を決定するための基礎を提供します。これらのデータの調査と理解に基づいて、スタンピングプロセスが不十分であることが判明した場合、そのパフォーマンスに影響を与えない場合は、プロセスの変更を容易にするために提唱されるべきであり、製品設計、スタンピングより完璧な効果を達成するために、プロセスの準備、金型の設計、および金型の製造をより適切に組み合わせます。
第二に、技術的および経済的な部品がより合理的なスタンピング プロセス スキームであると判断します。部品の形状、寸法精度、プロセス分析の表面品質要件に応じて、ブランキング、パンチング、曲げなどの基本プロセスの性質を決定します(この単純なプロセスの性質は、通常、要件から直接得ることができます決定する部品表の >; プロセス計算に従って、描画時間などのプロセス数を決定します; 各プロセスの変形特性に応じて、プロセス配置の順序を決定するためのサイズ要件、最初のパンチングの場合曲げ後または打ち抜き後の曲げ; 生産バッチと条件に応じて、複合スタンピングプロセス、連続スタンピングプロセスなどのプロセスの組み合わせを決定します。
第三に、金型の選択。プロセスの性質、プロセスの順序と組み合わせが決定されると、つまり、スタンピングプロセススキームが決定され、この時点で金型構造フォームのプロセスも決定されます (金型フォームの選択については、以下の説明を参照してください)。 .
第四に、必要なプロセス計算です。主に以下が含まれます:最も経済的な原則と材料の使用の合理的な決定の下でサンプルを配置するためのブランクサイズの計算。プレスを決定するために、パンチ圧力(パンチ力、曲げ力、引張力、除荷力、押し力、ブランクホルダー力などを含む)を計算します。偏心荷重によって金型の品質に影響を与えないように、金型の圧力中心を計算します。金型の主要部品(凹型、パンチ固定板、パッド、パンチなど)の寸法と、排出ゴムまたはスプリングの自由高さを計算または見積もります。凸型および凹型ダイのクリアランスを決定し、凸型および凹型ダイの作業部分のサイズを計算します。絞りダイスにブランクホルダーを使用するかどうか、絞りの数と中間を決定します。金型サイズ分布と半製品サイズの計算を処理します。
第五に、金型の全体的なデザイン。上記の分析と計算に基づいて、全体的な金型設計を実行できます。一般的には、まず構造をスケッチし、金型の閉じ高さを事前に計算して、金型の形状サイズを大まかに決定します。この時点で、各コンポーネントの構造を設計して、大まかなスキームを決定できます。これらのステップは、最適なソリューションを決定するために、相互に密接に関連し、統合され、補完されていることに注意してください。一般的には、部品構造の設計を考慮しながら全体設計を行います。順序は絶対ではありません。コンポーネント構造の設計には、主に次の内容が含まれます。
①作業部。パンチ、凹型、凸型、凹型などの構造形態は、一体型、組み合わせ型、はめ込み型、および固定型の決定です。
②部品を探す。位置決め板、バッフルピン(固定式・可動式)の使用など、その形態は多岐にわたり、状況に応じて選択・設計が可能です。順送型の場合は、イニシャルバッフルピン、ガイドピン、ディスタンスパンチ(サイドエッジ)を使用するかどうかも検討してください。
③装置の荷降ろしと押し込み。アンロードは一般に、リジッドとフレキシブルの 2 つの形式で使用されます。硬質印刷材料は通常、固定アンロードプレートの構造形式を採用し、柔軟なアンロード材料は通常、弾性要素としてスキンまたはスプリングを採用します (そのスプリングまたはゴムは設計および計算する必要があります)。
④ガイドパーツ。ガイド部品が必要かどうか、どのような形状のガイド部品を使用するかなど。ガイドポスト・ガイドを使用する場合は、ガイドポストの径と長さを決める必要があります。
⑤型枠の選定、取付、固定。
第六に、プレスを選択します。プレスの選定は金型設計の重要な部分であり、金型設計時にプレスの種類と仕様を決定する必要があります。プレスタイプの決定は、主にスタンピングプロセスの要件と金型の構造に依存します。
作業の流れ
1.ご注文受付--->2. 設計--->3. 図面・解の確認--->4.材料を準備する--->5.CNC--->6.CMM--->6. 組み立て--->7.CMM→8.検査--->9. (必要に応じて第 3 部検査)--->10. (社内/現場の顧客)--->11.梱包(木箱)--->12. 配送
リードタイムと梱包
3Dデザイン承認後45日
速達で5日:FedEx by Air
標準輸出木製ケース